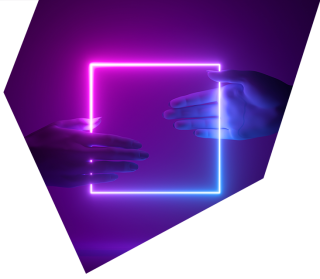
Procurement is a fundamental part of an organisation's operations, involving sourcing and acquiring goods and services from suppliers. However, the traditional procurement process often involves multiple inefficiencies and waste that could be reduced through the implementation of Lean methodology.
Lean methodology is an approach that focuses on streamlining processes, eliminating waste and maximising value. It was originally developed by Toyota and has been adopted by many organisations as a way to optimise operations and increase efficiency. When applied to procurement, Lean methodology can help organisations reduce costs, improve quality and, increase collaboration with suppliers.
Here are some ways that organisations can implement Lean methodology in their procurement functions:
The implementation of Lean methodology in procurement can bring several benefits to the organisation. Reduced lead times, improved quality, and lower costs are just a few of the benefits of implementing Lean methodology in procurement.
In conclusion. The implementation of Lean methodology in procurement can help increase efficiency, eliminate waste, and maximise value. By standardising processes, eliminating unnecessary steps, improving supplier collaboration, implementing a digital system, and tracking performance metrics, organisations can streamline their procurement processes and reap the benefits of a Lean approach.